Downhole Drilling Tool
Electrical Connectors
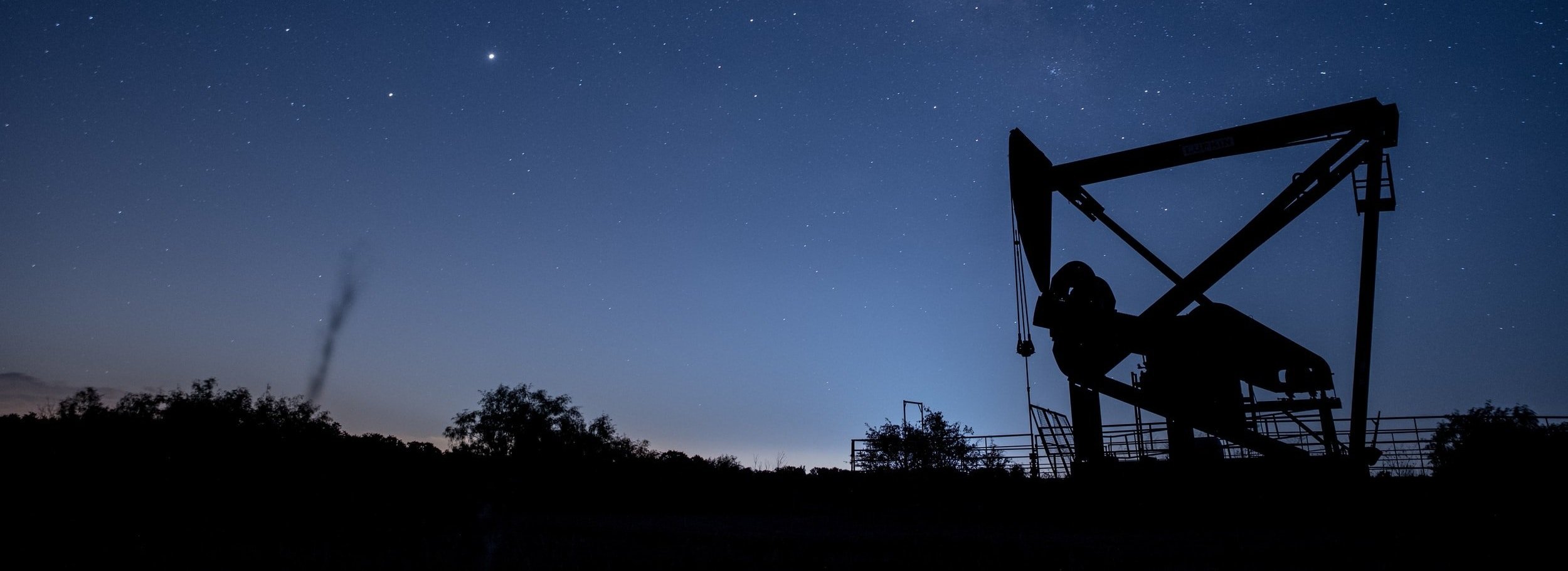
I kicked off my career by digging deep.
While at Greene, Tweed & Co. in Houston, TX, I was fortunate to be a part of their Rotation Engineer Program, where over a 2 year period, I rotated through different departments (design, processing, and quality) every 6 months. The program exposed me to several roles where I designed, built, sustained, and improved upon seals, bearings, and electro-mechanical connectors for downhole drilling tools.
Since this was early in my career, I was fortunate to learn a lot about sealing various fluids and the behavior of rubber and plastic at high temperatures. These applications provided an interesting challenge because the temperatures and pressures needed for sealing were extremely high; from -20°F up to 500°F, and up to 30,000 psi!
Examples of Plastic and Elastomer Seals
I rotated through many departments, including Process Engineering and Quality Engineering, where I gained an RJG’s Molding Essentials certification and a Lean Six Sigma Green Belt. I was eventually chosen for the design department, where I had the opportunity to work directly with and design some injection molding tools as well. I honed my skills in drafting engineering drawings, in GD&T, FEA, and working with multiple parties to achieve cost effective, desired results.
During my time in the design department, I was placed on the New Product Development team as the engineering lead, and was tasked with working on special projects for customers that would require more R&D work than the usual design requests.
Greene, Tweed had just launched their latest material, Arlon® 3000XT, which was instrumental in building seals and connectors that could withstand the highest temperatures and pressures. Many of the designs I created were the first of their kind, especially in testing the process parameters, wall thickness, and geometries that could be achieved with this new material. Any of the black connectors you see on this page are made from Arlon® 3000XT, and I’m proud to say that I designed some of them!
One of many connectors I designed!
Connectors after Pressure Testing